Solids and Slurries
When liquids contain solids and slurries the specific gravity of the mixture needs to be considered. The size and type of slurry will affect the abrasiveness and the type of slurry pump that is suitable. This section details methods to calculate specific gravity by concentration of solids, provides hardness values of common solids, and presents the class of pump appropriate for slurry types.
Useful Formulas
a) The formula for specific gravity of a solids-liquids mixture or slurry, Sm is:
(Eq. 2.B.1)
Where:
- Sm = specific gravity of mixture or slurry
- Sl = specific gravity of liquid phase
- Ss = specific gravity of solids phase
- Cw = concentration of solids by weight
- Cv = concentration of solids by volume
Example: If the liquid has a specific gravity of 1.2 and the concentration of solids by weight is 35% with the solids having a specific gravity of 2.2 then:
b) Basic relationships among concentration and specific gravities of solid liquid mixtures are shown below.
Where pumps are to be applied to mixtures which are both corrosive and abrasive, the predominant factor causing wear should be identified and the materials of construction selected accordingly. This often results in a compromise and in many cases can only be decided as a result of test or operational experience. ANSI/HI 12.1-12.6 – Rotodynamic Centrifugal Slurry Pumps contains more information regarding the operation and applications of slurry pumps.
For any slurry pump application a complete description of the mixture components is required in order to select the correct type of pump and materials of construction.
(Eq. 2.B.2)
(Eq. 2.B.3)
A nomograph for the relationship of concentration to specific gravity of dry solids in water is shown in Figure 2.B.3.
c) Slurry flow requirements can be determined from the expression:
(Eq. 2.B.4)
Where:
- Qm = slurry flow (gallons per minute)
- 1 ton = 2000 lbs
Example: If 2,400 tons of dry solids is processed in 24 hours in water with a specific gravity of 1.0 and the concentration of solids by weight is 30% with the solids having a specific gravity of 2.7 then:
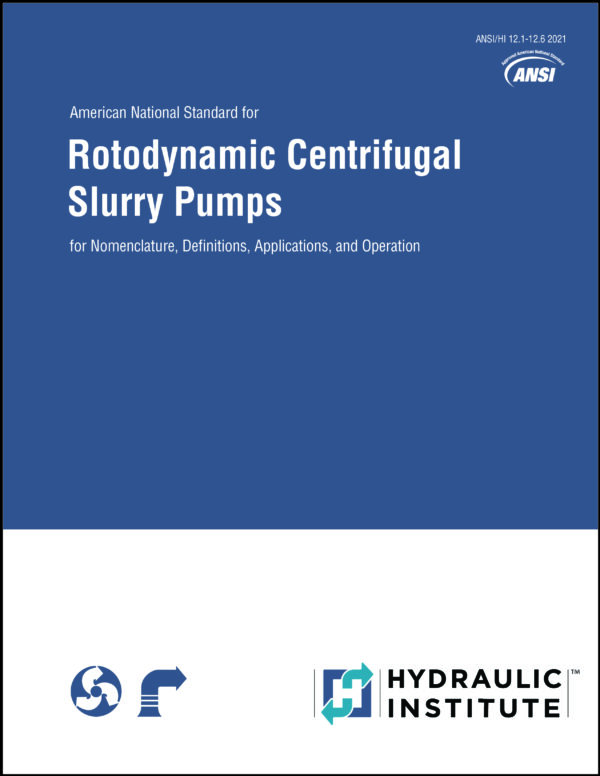
Rotodynamic Centrifugal Slurry Pumps
This standard offers a basic educational overview on rotodynamic (centrifugal) slurry pumps, design and application considerations related to the selection of the right pump for a specific industry including pump installation as well as operation and maintenance procedures.
d) Abrasive wear:
Wear increases rapidly when the particle hardness exceeds that of the metal surfaces being abraded. Always select metals with a higher relative hardness to that of the particle hardness. There is little to be gained by increasing the hardness of the metal unless it can be made to exceed that of the particles. The effective abrasion resistance of any metal will depend on its position on the mohs or knoop hardness scale. The relationships of various common ore minerals and metals is shown in Figure 2.B.2.
Wear increases rapidly when the particle size increases. The life of the pump parts can be extended by choosing the correct materials of construction.
Sharp angular particles cause about twice the wear of rounded particles.
Austenitic manganese steel is used when pumping large dense solids where the impact is high.
Hard irons are used to resist erosion and to a lesser extent impact wear.
Elastomeric materials are used when pumping concentrations of fine material but total head is usually restricted to about 100 ft. per stage.
Castable ceramic materials have excellent resistance to cutting erosion but impeller tip velocities are usually restricted to 100 ft/s.
Classification of pumps according to particle size is shown in Figure 2.B.4.
Approximate Comparison of Hardness Values of Common Ores and Minerals [1]
Nomograph of the Relationship of Concentration to Specific Gravity in Aqueous Slurries [2]
Classification of Pumps According to Solid Size [3]
References
- Hydraulic Institute, Engineering Data Book, Second Edition, 1990, Figure IIB-4.
- Hydraulic Institute, Engineering Data Book, Second Edition, 1990, Figure IIB-5.
- Hydraulic Institute, Engineering Data Book, Second Edition, 1990, Figure IIB-6.
Last updated on April 19th, 2024