Losses With Paper Stock
I. Introduction
In any stock piping system, the pump provides flow and develops hydraulic pressure (head) to overcome the differential in head between two points. This total head consists of pressure head, static head, velocity head and total frictional head produced by friction between the pulp suspension and the pipe, bends, and fittings. The total frictional head is the most difficult to determine because of the complex, non-linear nature of the frictional loss curve. This curve can be affected by many factors.
The following analytical method for determining pipe frictional losses is based on the recently published TAPPI Technical Information Sheet (TIS) 408-4 [1] and is applicable to stock consistencies (oven-dried) from 2 to 6 percent. Normally, stock consistencies of less than 2% (oven-dried) are considered to have the same frictional losses characteristic as water. This paper only applies to systems using centrifugal pumps which is normal for these consistencies. The method for determining the frictional losses of pulp suspensions in pipe, as presented here, is intended to supersede the various methods previously issued.
II. Background
Figures 3.E.1 (chemical pulp) and 3.E.2 (mechanical pulp) show typical frictional loss curves for two different consistencies (C2 > C1).
Friction loss curve for chemical pulp C2 > C1
Friction loss curve for mechanical pulp C2 > C1
The frictional loss curve for chemical pulp can be conveniently divided into three regions, as illustrated by the shaded areas of Figures 3.E.3 and 3.E.4.
Friction loss curve for chemical pump, shaded to show individual regions
Friction loss curve for mechanical pump, shaded to show individual regions
Regions shown in Fig. 3.E.3 may be described as follows:
Region 1: (Curve AB) is a linear region where frictional loss for a given pulp is a function of consistency, velocity, and pipe diameter. The velocity at the upper limit of this linear region (Point B) is designated vmax.
Region 2: (Curve BCD) shows an initial decrease in frictional losses (to Point C) after which the frictional losses again increase. The intersection of the pulp frictional loss curve and the water frictional loss curve (Point D) is termed the onset of drag reduction. The velocity at this point is designated vw.
Region 3: (Curve DE) shows the frictional loss curve for pulp fiber suspensions below the water curve. This is due to a phenomenon called drag reduction. [2] describes the mechanisms which occur in this region.
Regions 2 and 3 are separated by the frictional loss curve for water, which is a straight line with a slope approximately equal to 2.
The frictional loss curve for mechanical pulp, as illustrated in Figure 3.E.4 (right), is divided into only two regions:
Regions 1 and 3: For this pulp type, the frictional loss curve crosses the water curve vw and there is no true vmax·
III. Design Parameters
To determine the pipe frictional loss component for a specified design basis (usually daily mass flow rate), the following parameters must be defined:
a) Pulp Type — Chemical or mechanical pulp, long or short fibered, never dried or dried and reslurried, etc. This is required to choose the proper coefficients which define the pulp friction curve.
b) Consistency, C (oven-dried) — Often a design constraint in an existing system. NOTE: If air-dried consistency is known, multiply by 0.9 to convert to oven-dried consistency.
c) Internal pipe diameter, D — Lowering D reduces initial capital investment, but increases pump operating costs. Once the pipe diameter is selected, it fixes the velocity for a prespecified mass flow rate.
d) Bulk velocity, v — Usually based on a prespecified daily mass flow rate. Note that both v and D are interdependent for a constant mass flow rate.
e) Stock temperature, T — Required to adjust for the effect of changes in viscosity of water (the suspending medium) on pipe frictional losses.
f) Freeness — Used to indicate the degree of refining or to define the pulp for comparison purposes.
g) Pipe material — Important to specify design correlations and compare design values.
IV. Pipe Friction Estimation Procedure
The bulk velocity (v) will depend on the daily mass flow rate and the pipe diameter (D) selected. The final value of v can be optimized to give the lowest capital investment and operating cost with due consideration of future demands or possible system expansion.
The bulk velocity will fall into one of the regions previously discussed. Once it has been determined in which region the design velocity will occur, the appropriate correlations for determining pipe frictional loss value(s) may be selected. The following describes the procedure to be used for estimating pipe frictional losses in each of the regions.
Region 1: The upper limit of Region 1 in Figure 3 (Point B) is designated vmax. The value of vmax is determined using Equation (3.E.1) and data given in Table I.
(Eq. 3.E.1)
where:
- K' = numerical coefficient (constant for a given pulp), obtained from Table I
- C = consistency (oven-dried, expressed as a percentage, not decimally), 2-6% limit.
- σ = exponent (constant for a given pulp), obtained from Table I
The following is data for use with Equation (3.E.1) to determine velocity limit, vmax·
Table I
Pulp Type (5) | Pipe Material | K | σ |
---|---|---|---|
Unbeaten aspen sulfite never dried (2) | Stainless Steel | 0.85 | 1.6 |
Long fibered kraft never dried CSF = 725 (6) (2) | PVC | 0.98 | 1.85 |
Long fibered kraft never dried CSF = 725 (6) (2) | Stainless Steel | 0.89 | 1.5 |
Long fibered kraft never dried CSF = 650 (6) (2) | PVC | 0.85 | 1.9 |
Long fibered kraft never dried CSF = 550 (6) (2) | PVC | 0.75 | 1.65 |
Long fibered kraft never dried CSF = 260 (6) (2) | PVC | 0.75 | 1.8 |
Bleached kraft pine dried and reslurried (6) (2) | PVC | 0.79 | 1.5 |
Bleached kraft pine dried and reslurried (6) (2) | Stainless Steel | 0.59 | 1.45 |
Long fibered kraft dried and reslurried (6) (2) | PVC | 0.49 | 1.8 |
Kraft birch dried and reslurried (6) (2) | PVC | 0.69 | 1.3 |
Stone groundwood CSF = 114 (2) | PVC | 4.0 | 1.40 |
Refiner groundwood CSF = 150 (2) | PVC | 4.0 | 1.40 |
Newsprint broke CSF = 75 (2) | PVC | 4.0 | 1.40 |
Refiner grouridwood (hardboard) (2) | PVC | 4.0 | 1.40 |
Refiner groundwood (insulating board) (2) | PVC | 4.0 | 1.40 |
Hardwood NSSC CSF = 620 (2) | PVC | 0.59 | 1.8 |
Unbleached sulfite (1) | Copper | 0.98 | 1.2 |
Bleached sulfite (1) | Copper | 0.98 | 1.2 |
Kraft(1) | Copper | 0.98 | 1.2 |
Bleached straw (1) | Copper | 0.98 | 1.2 |
Unbleached straw (1) | Copper | 0.98 | 1.2 |
Cooked groundwood (1) | Copper | 0.75 | 1.8 |
Soda (1) | Steel | 4.0 | 1.4 |
NOTES:
- Estimates for pulps based on published literature.
- Original data obtained in stainless steel and PVC pipe.
- Stainless steel may be hydraulically smooth although some manufacturing processes may destroy the surface and hydraulic smoothness is lost. PVC is taken to be hydraulically smooth pipe.
- For cast iron and galvanized pipe, the K9 values will be reduced. No systematic data are available for the effects of surface roughness.
- If pulps are not identical to those shown, some engineering judgement is required.
- Wood is New Zealand Kraft pulp.
If the proposed design velocity (v) is less than vmax, the value of flow resistance (Δh/L) may be calculated using equation 3.E.2 and data given in Table II and the appendices.
(Eq. 3.E.2)
where:
- F = factor to correct for temperature, pipe roughness, pulp type, freeness, or safety factor (refer to Appendix A)
- K = numerical coefficient (constant for a given pulp), obtained from Table II
- v = bulk velocity (ft/s)
- C = consistency (oven-dried, expressed as a percentage, not decimally), 2-6% limit
- D = pipe inside diameter (in), and
- α,β,γ = exponents (constant for a given pulp), obtained from Table II
For mechanical pulps, there is no true vmax· The upper limit of the correlation equation (Equation (3.E.2)) is also given by Equation (3.E.1) in this case, the upper velocity is actually vw·
Region 2: The lower limit of Region 2 in Figure 3 (Point B) is vmax and the upper limit (Point 0) is vw. The velocity of the stock at the onset of drag reduction is determined using equation 3.E.3.
(Eq. 3.E.3)
where:
- C = consistency (oven-dried, expressed as a percentage, not decimally).
If v is between vmax and vw, Equation (3.E.2) may be used to determine ΔH/L at the maximum point (vmax)· Because the system must cope with the worst flow condition, ΔH/L at the maximum point (v max) can be used for all design velocities between vmax and vw·
Region 3: A conservative estimate of frictional losses is obtained by using the water curve. (Δh/ L)w can be obtained from a Friction Factor vs. Reynolds Number plot ([3],for example), or approximated from the following equation (based on the Blasius equation).
(Eq. 3.E.4)
where:
- v = bulk velocity (ft/s), and
- D = pipe diameter (in.)
Previously published methods for calculating pipe frictional losses of pulp suspensions gave a very conservative estimate of head loss. The method just described gives a more accurate estimate of head loss due to friction, and has been used successfully in systems in North America and world-wide.
Pertinent equations, in addition to those herein presented, are located in Appendix A. Example problems are located in Appendix B.
-
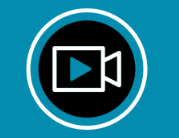
Preferred and Allowable Operating Regions for Rotodynamic Pumps to Maximize Reliability: 1-Part On-Demand Webinar
This webinar covers how the Preferred Operating Region (POR) and Allowable Operating Region (AOR) are defined for centrifugal, mixed and axial flow pumps and their impact on efficiency and reliably. Curve shape, hydraulic loading, temperature rise, vibration/noise, suction recirculation, priming, NPSH margin and more will be discussed related to a pumps AOR as well as methods to ensure operating in the AOR will be presented. This webinar is a must for pump end users, application engineers, pump system designers, specifying engineers and pump service providers.
V. Head Losses in Valves, Bends and Fittings
The frictional head losses of pulp suspensions in valves, bends and fittings may be determined from the basic equation for head loss, provided in Fluid Flow – General.
Values of K for the flow of water through various types of bends and fittings are tabulated in numerous reference sources ([3], for example). The loss coefficient for valves may be obtained from the valve manufacturer.
The loss coefficient for pulp suspensions in a given bend or fitting generally exceeds the loss coefficient for water in the same bend or fitting. As an approximate rule, the loss coefficient (K) increases 20 percent for each 1 percent increase in oven-dried stock consistency. Please note that this is an approximation; actual values of K may differ, depending on the type of bend or fitting under consideration (4).
The following is data for use with Equation (3.E.2) to determine head loss, ΔH/L.
Table II
Pulp Type | K | α | β | γ (3), (4) |
---|---|---|---|---|
Unbeaten aspen sulfite never dried (2) | 5.30 | 0.36 | 2.14 | -1.04 |
Long fibered kraft never dried CSF = 725 (5) (2) | 11.80 | 0.31 | 1.81 | -1.34 |
Long fibered kraft never dried CSF = 650 (5) (2) | 11.30 | 0.31 | 1.81 | -1.34 |
Long fibered kraft never dried CSF = 550 (5) (2) | 12.10 | 0.31 | 1.81 | -1.34 |
Long fibered kraft never dried CSF = 260 (5) (2) | 17.00 | 0.31 | 1.81 | -1.34 |
Bleached kraft pine dried and reslurried (5) (2) | 8.80 | 0.31 | 1.81 | -1.34 |
Long fibered kraft dried and reslurried (5) (2) | 9.40 | 0.31 | 1.81 | -1.34 |
Kraft birch dried and reslurried (5) (2) | 5.20 | 0.27 | 1.78 | -1.08 |
Stone groundwood CSF = 114 (2) | 3.81 | 0.27 | 2.37 | -0.85 |
Refiner groundwood CSF = 150 (2) | 3.40 | 0.18 | 2.34 | -1.09 |
Newsprint broke CSF = 75 (2) | 5.19 | 0.36 | 1.91 | -0.82 |
Refiner grouridwood (hardboard) (2) | 2.30 | 0.23 | 2.21 | -1.29 |
Refiner groundwood (insulating board) (2) | 1.40 | 0.32 | 2.19 | -1.16 |
Hardwood NSSC CSF = 620 (2) | 4.56 | 0.43 | 2.31 | -1.20 |
Unbleached sulfite (1) | 12.69 | 0.36 | 1.89 | -1.33 |
Bleached sulfite (1) | 11.40 | 0.36 | 1.89 | -1.33 |
Kraft(1) | 11.40 | 0.36 | 1.89 | -1.33 |
Bleached straw (1) | 11.40 | 0.36 | 1.89 | -1.33 |
Unbleached straw (1) | 5.70 | 0.36 | 1.89 | -1.33 |
Cooked groundwood (1) | 6.20 | 0.43 | 2.31 | -1.20 |
Soda (1) | 6.50 | 0.36 | 1.85 | -1.04 |
NOTES:
- Estimates for pulps based on published literature.
- Original data obtained in stainless steel and PVC pipe (7, 8, 9).
- No safety factors are included in the above correlations.
- The frictional loss depends considerably on the condition of the inside of the pipe surface (10).
- Wood is New Zealand Kraft pulp.
Appendix A
The following gives supplemental information to that provided in the main text.
1) Rate of flow, Q
(Eq. 3.E.5)
where:
- T.P.D. = mill capacity (short tons per day)
and
- C = consistency (oven-dried, expressed as a percentage, not decimally).
2) Bulk velocity, v
(Eq. 3.E.6)
(Eq. 3.E.7)
where:
- Q = rate of flow (gpm)
- A = inside area of pipe (in^2^)
- D = inside diameter of pipe (in)
3) Multiplication Factor, F (included in Equation (3.E.2))
(Eq. 3.E.8)
where:
- F1 is the correction factor for temperature. Friction loss calculations are normally based on a reference pulp temperature of 95°F. The flow resistance may be increased or decreased by 1 percent for each 1.8°F below or above 95°F, respectively. This may be expressed as follows (where T = pulp temperature (°F)):
(Eq. 3.E.9)
F2 is the correction factor for pipe roughness. This factor may vary due to manufacturing processes of the piping, surface roughness, age, etc. Typical values for PVC are F2=1.0 and stainless steel piping are F2=1.25 (please note that these are typical values; experience and/or additional data may modify these factors):
F3 is the correction factor for pulp type. Typical values are 1.0 for pulps that have never been dried and reslurried and **0.8 for pulps that have been dried and reslurried.
Note: This factor has been incorporated in the numerical coefficient, K, for the pulps listed in Table II. When using Table II, F3 should not be used.
F4 is the correction factor for beating. Data have shown that progressive beating causes, initially, a small decrease in frictional losses, followed by a substantial increase. For a kraft pine pulp initially at 725 CSF and F4 = 1.0, beating caused the freeness to decrease to 636 CSF and F4 to decrease to 0.96. Progressive beating decreased the freeness to 300 CSF and increased F4 to 1.37 (see K values in Table II). Some engineering judgement may be required.
F5 is the design safety factor. This is usually specified by company policy with consideration given to future requirements.
Appendix B
The following is an example that illustrates the method for determining pipe frictional losses in each of the three regions shown in Figure 3.E.3.
Example
Determine the frictional loss (per 100 ft of pipe) for 2% oven-dried bleached kraft pine, dried and reslurried, through 6 inch schedule 40 stainless steel pipe (inside diameter = 6.065 in). The pulp temperature is 90°F, the flow rate 1100 U.S. GPM.
Solution:
a) The bulk velocity is:
b) It must be determined in which region (1, 2 or 3) this velocity falls. To obtain an initial indication, determine Vmax.
Where: - K' = 0.59 (from Table 3.E.1), - σ = 1.45 (from Table 3.E.1),
c) Since v exceeds vmax, Region 1 (the linear region) is eliminated. To determine whether v lies in Region 2 or 3, the velocity at the onset of drag reduction, vW, must be calculated.
d) v exceeds vw, indicating that it falls in Region 3. The frictional loss is calculated as that of water flowing at the same velocity.
This will be a conservative estimate, as the actual frictional loss curve for pulp suspensions under these conditions will be below the water curve.
References
- TAPPI Technical Information Sheet (TIS) 408-4. Technical Association of the Pulp and Paper Industry, Atlanta. Georgia (1981).
- K. Molier and G. G. Duffy. TAPPI 61 , 1, 63 (1978).
- Hydraulic Institute Engineering Data Book, First Edition. Hydraulic Institute. Cleveland. Ohio (1979).
- K. Molier and G. Elmquist. TAPPI 63, 3, 101 (1980).
- W. Brecht and H. Heller. TAPPI 33, 9, 14A (1950).
- R. E. Durst and L. C. Jenness. TAPPI 39, 5, 277 (1956).
- K. Molier. G. G. Duffy and A. L. Titchener. APPITA 26, 4, 278 (1973).
- G. G. Duffy and A. L. Tichener. TAPPI 57, 5, 162 (1974).
- G. G. Duffy, K. Molier, P. F. W. Lee and S. W. A. Mine, APPITA 27, 5, 327 (1974).
- G. G. Duffy, TAPPI 59, 8, 124 (1976).
- G. G. Duffy. Company Communications Goulds Pumps. Inc. (1980-1981).
Last updated on June 28th, 2019